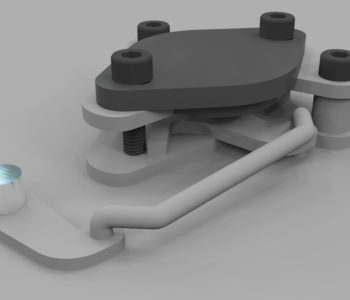
Quarinjection Throttle Position Sensor
I chose to re-use the current Solex 28/32 PDSIT-4 carburetor rather than purchase a new throttle body. The carbs role to meter and deliver fuel will now be done by the fuel injectors, so the carb only needs to function as a throttle plate and provide the ECU with the throttle position.
I stripped down the existing carb by removing the fuel bowl, automatic choke and venturi and then used epoxy to fill any unneeded fuel or air passages.
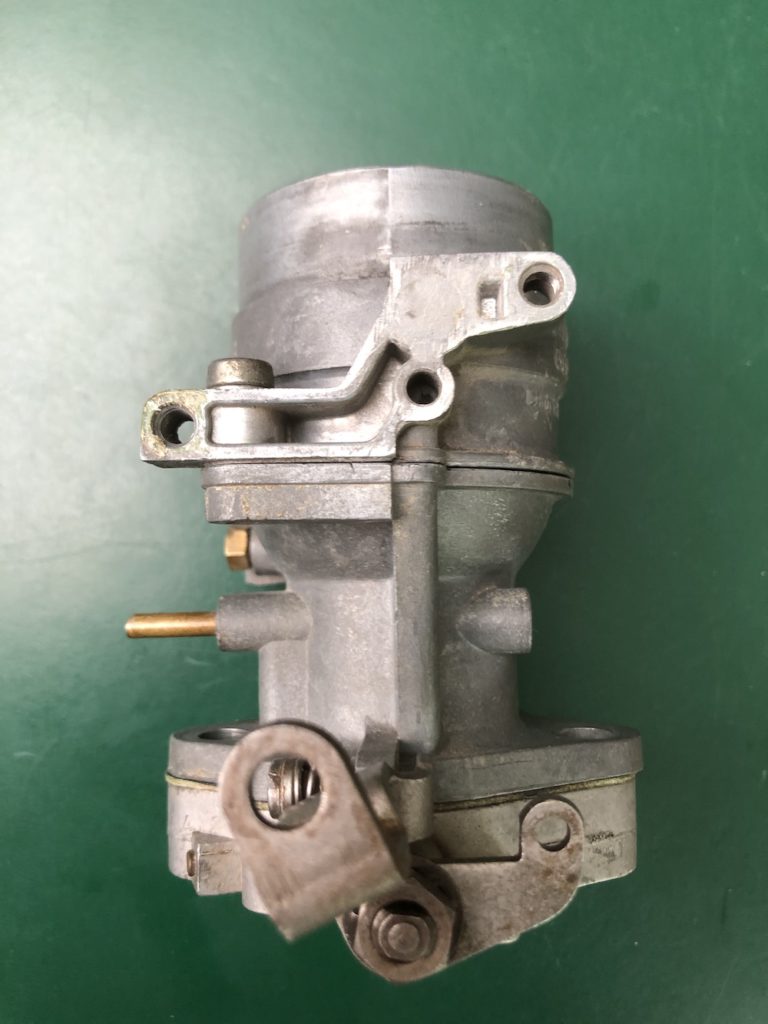
The Throttle Position Sensor (TPS) is a potentiometer that rotates the same ~90 degrees as throttle plate. The position is then read by the ECU. The task is to interface the current throttle movement to the TPS which is normally connected directly to the throttle shaft on the opposite side to the cable/linkage. On the Solex the plate turns the opposite direction to the TPS I have (from a Honda throttle body $10), so it has to mount on the same side as the linkage (or geared to the shaft) . Space is also very limited around the manifold mounted carb.
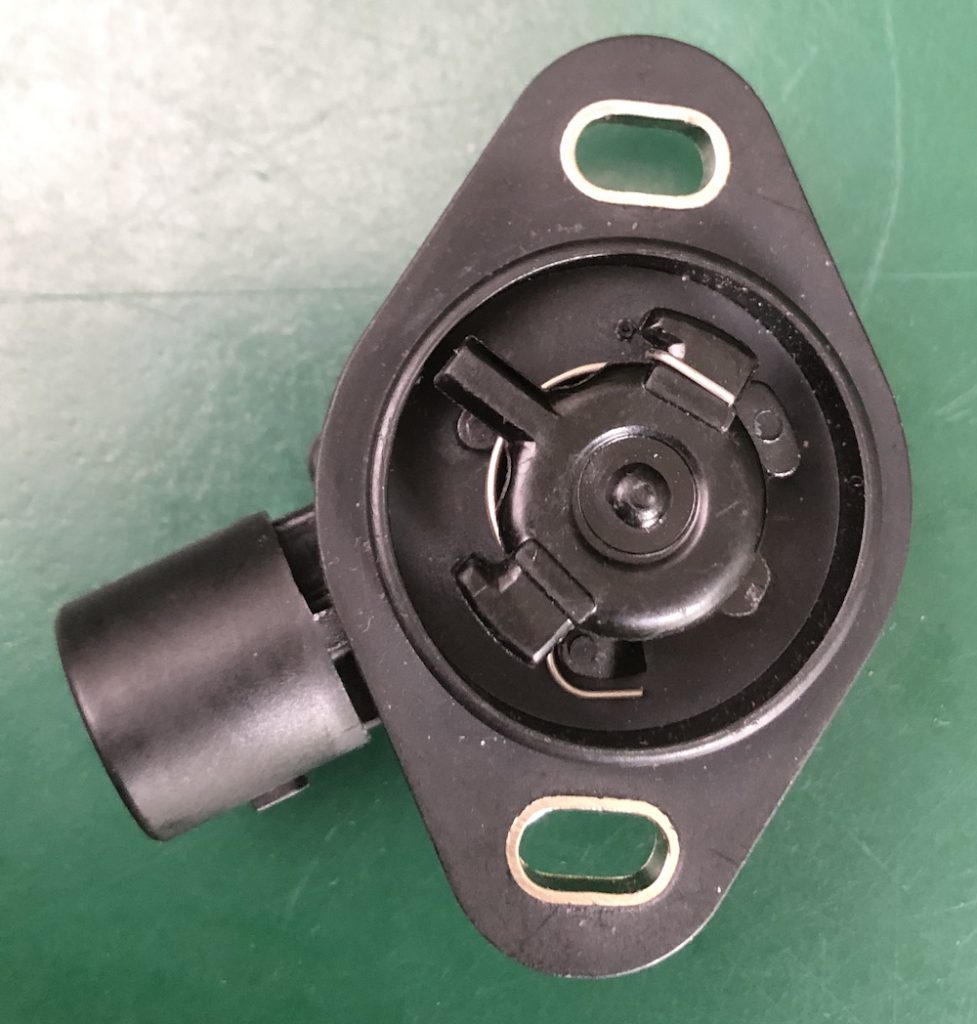
There are existing threaded mounting holes where the old choke was that I can use to attach the TPS. I designed a mount and lever system that uses the choke lever on the throttle shaft.
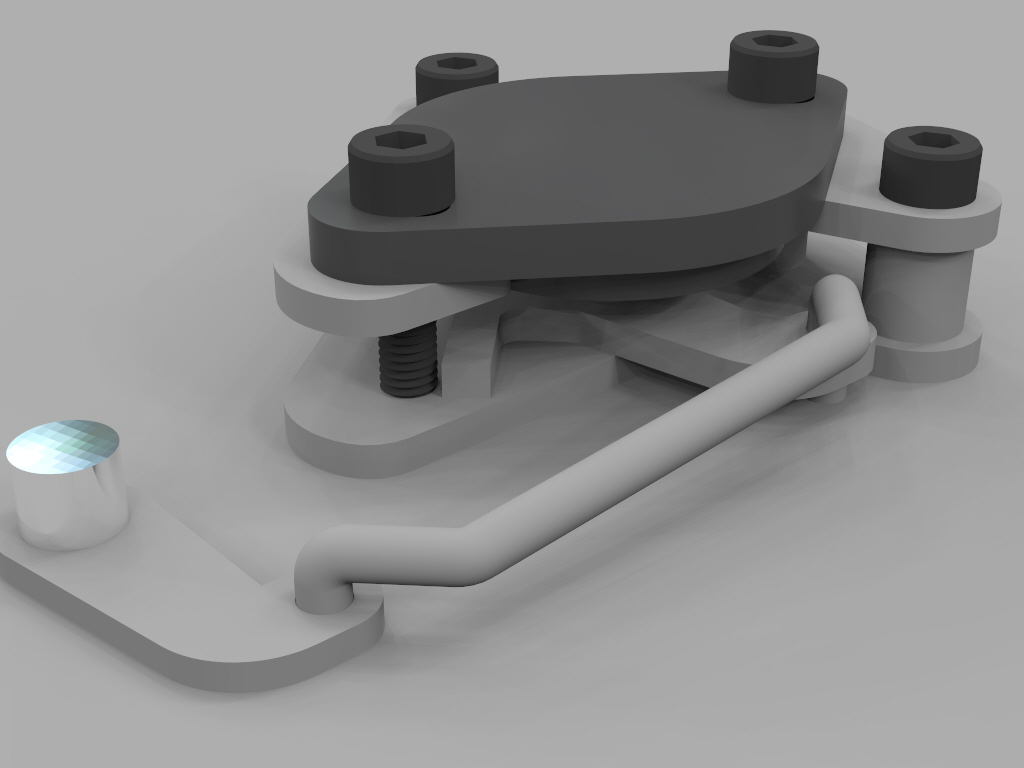
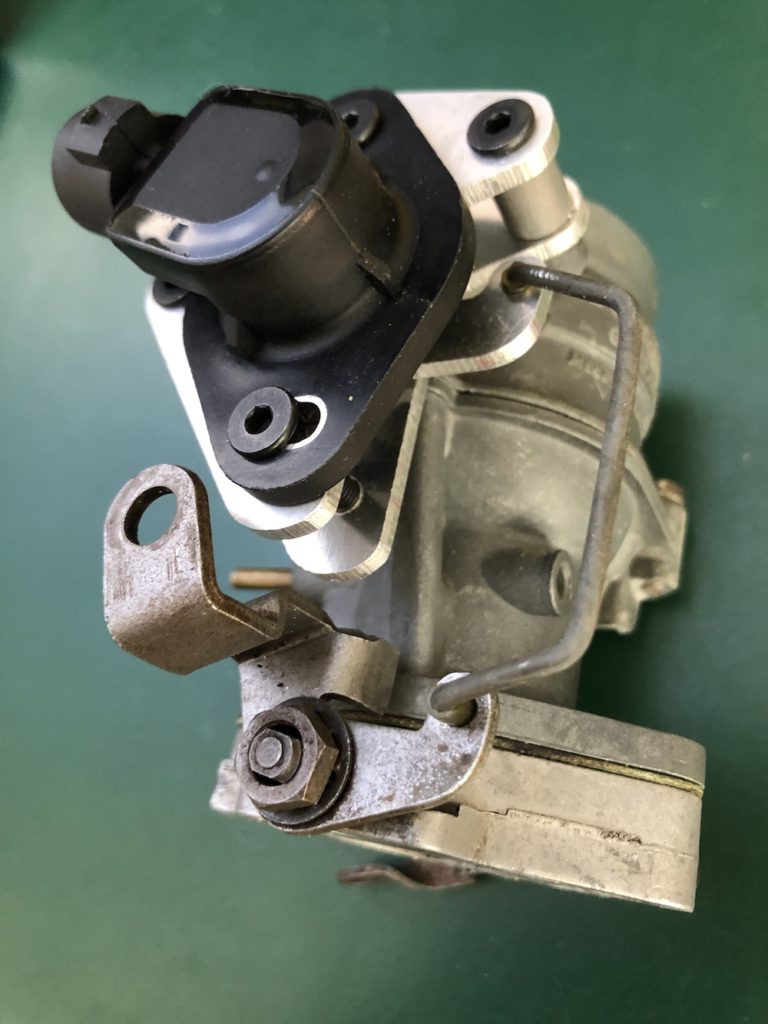
Retrospect:
Milling: I was very pleased with the milling now that I have the feeds and speeds dialed in. The dimensions of the holes were slightly small which means I probably have a calibration issue with grbl. I had my doubts about routing a 4.7mm hole with a 3.175mm mill. It works without air clearing but does regrind some chips. I am not doing finishing passes as the double stick mounting tape I’m using can’t take the force after it’s cut free from the sheet.
Design: Version 1 worked as planned and I didn’t have to redesign or recut anything. The full range of motion was just possible with the design, so I should have rotated the lever another 5 degrees counter clockwise. 3003 aluminum is too soft (“tends to be gummy when machined“) for tapping and just kind of smears into a badly formed thread. Next time I’ll use brass or steel press fit inserts. The tapped holes on the carb were metric but done in the 60’s before there were standard sizes, so they are an odd M5x0.75; I retapped these holes to M5x0.80 without losing much integrity. I should have modeled the full throttle lever as it is very close to the lower low-profile bolt for the TPS (there is another lever on the opposite side of the throttle shaft which I may use instead). This is a temporary solution just to get the system to work and then I’ll redesign the entire inefficient intake manifold.
Overall success! On to other components…